In this age of rampant industrialization, sometimes it’s worthwhile to stop and think of the ecological impact. The carbon footprint we leave today will impact the tomorrow greatly. Carbon fuel and plastic overuse, recycling imbalance and toxication of air, water and earth are some intriguing complications of the contemporary world.
Besides traditional ways like afforestation, lifestyle changes and use green energy, some ray of hope can be seen in the evolution of counter-pollutant technology. These are aimed at reducing the number of pollutants in the environment while boosting the prospects of cleaner energy.
The direst need of the hour is reducing the amount of plastic and carbon based fuel usage. The tyre to oil machine is simple and easy to set up.
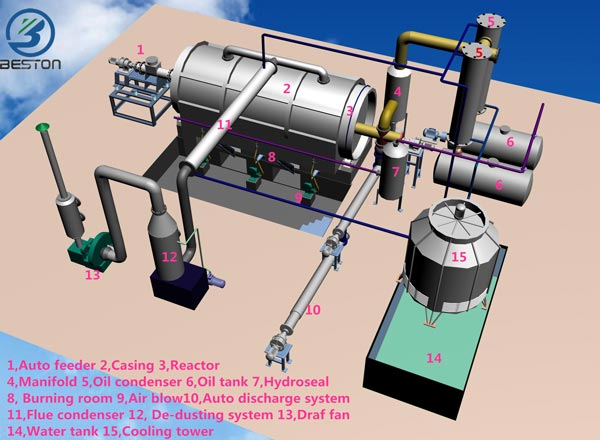
Pyrolysis of plastic and rubber items like tires is the best way to get rid of these harmful nondegradable pollutants. Pyrolysis means breaking down big chains of carbon molecules into simple carbon atoms, without emitting the harmful components into the air.
The products that are obtained at the end of the process are fuel oil, pyrolysis oil, carbon black and hydrocarbon gas. These have great industrial applications. The fuel obtained from the pyrolysis machine can be easily be used in low RPM power generators and industrial burners like steam boilers, thermic fluid heaters, melting furnaces, hot air generators, etc.
The whole plastic into fuel machine design consists of three main sections:
· The Pyrolysis reactor
· Char combustor
· Fuel Oil Condenser
The pyrolysis reactor is where the actual breakdown of plastic and rubber occur. It consists of the main reactor chamber, a catalytic chamber, pressure manipulators and heating systems. The main feed is converted into a slug and passed into the next section through a transmission device.
As the slug passes on to the next part, it is cooled down gradually inside a cooling tube, while being mixed with chemicals to make separation easier. The slug is passed through different filters to separate the oil part from the solid carbon residue. The carbon is collected by charring it thoroughly to extract any leftover fuel oil. The solid carbon residue is stored in a carbon container. Find high-quality machine from Beston Group.
The liquid oil part moves on to the fuel oil condenser unit, where an elaborate system of oil-water separators and oil condensers are used to obtain high octane fuel. The final fuel oil is segregated into two tanks. One is the light fuel oil tank and the other is heavy fuel oil tank.
Other than these, a typical tyre pyrolysis plant design will also include some safety device, a vacuum cleaning system, and a de-dusting system. There may be other variation on continuous feed system or batch feed models, but this is the basic plastic into fuel oil pyrolysis plant design.